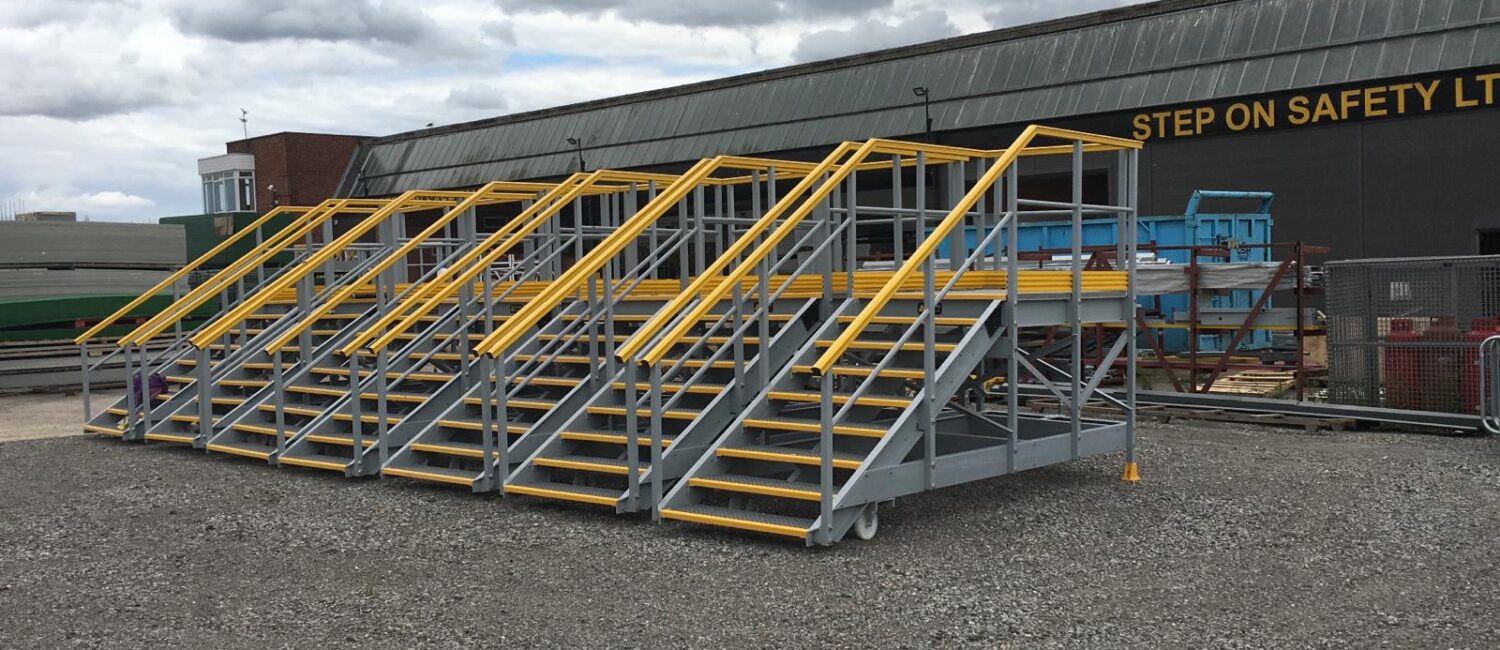

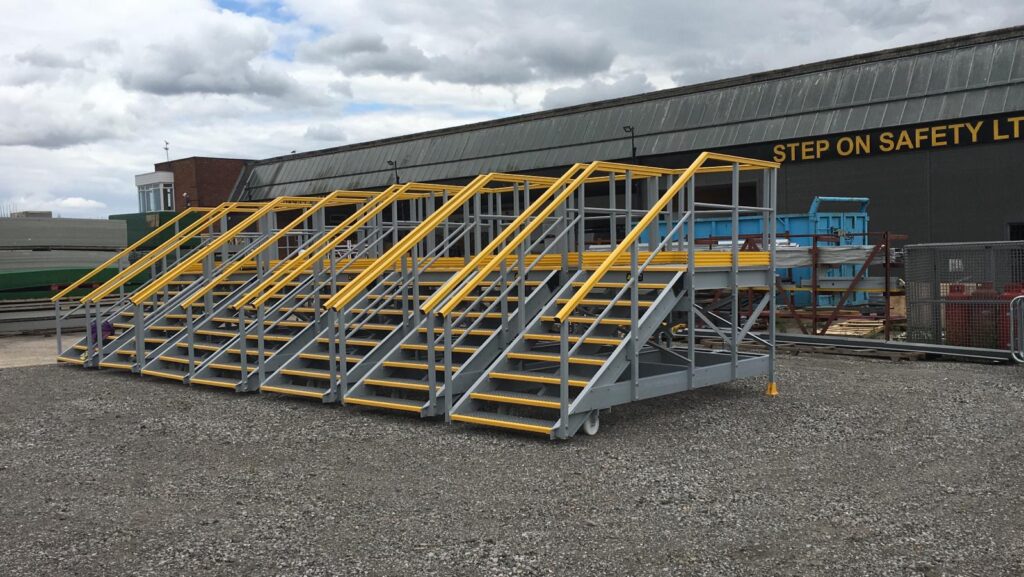
Repairing GRP Onsite
Two years ago when London Energy chose to replace the steel steps at their recycling sites with smart new GRP versions, they did so for many reasons. The obvious ones were that the new Mobile Access Platforms are easier to manoeuvre, anti-slip, low maintenance and hardwearing – but there was another crucial part of the decision: how easy it is to make GRP repairs.
When the old steel steps were battered, the frames, handrail and even the stair treads would bend and twist, sometimes leaving them unstable and unsafe. They then had to be scrapped or sent away for repair. The new GRP versions flex and spring back under most forces but, if sufficient pressure or impact is applied, it cracks. If that happens, the modular design allows you to simply remove the damaged part and bolt on a new one. What’s more, these GRP repairs can be done on site, taking the staircase out of circulation for just hours – not weeks – minimising disruption.
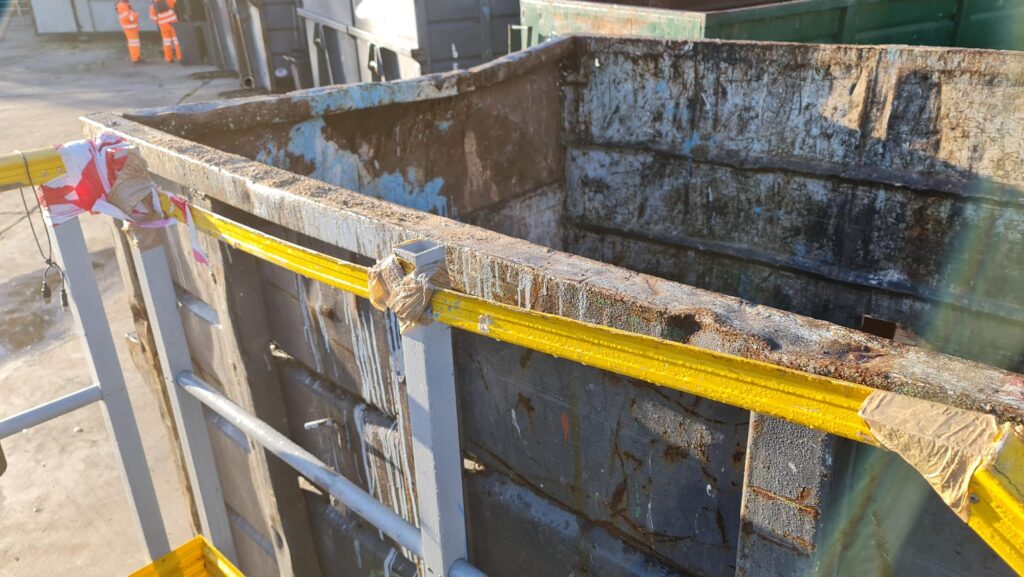
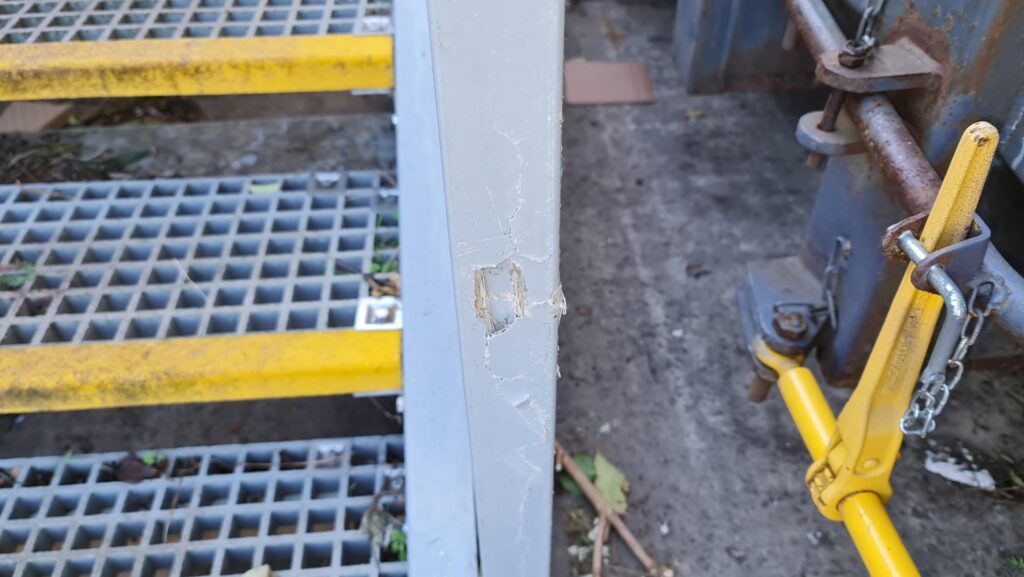
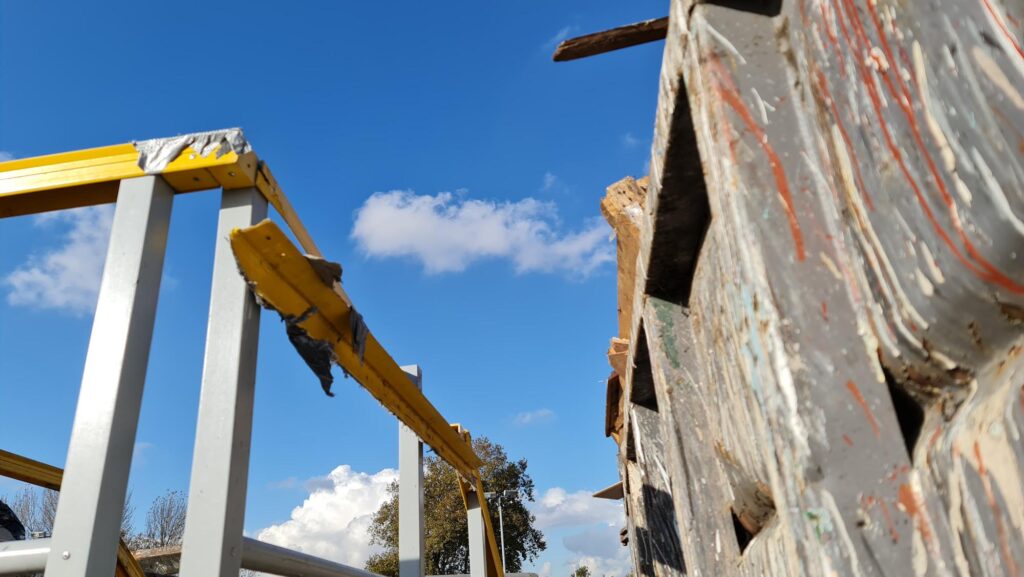
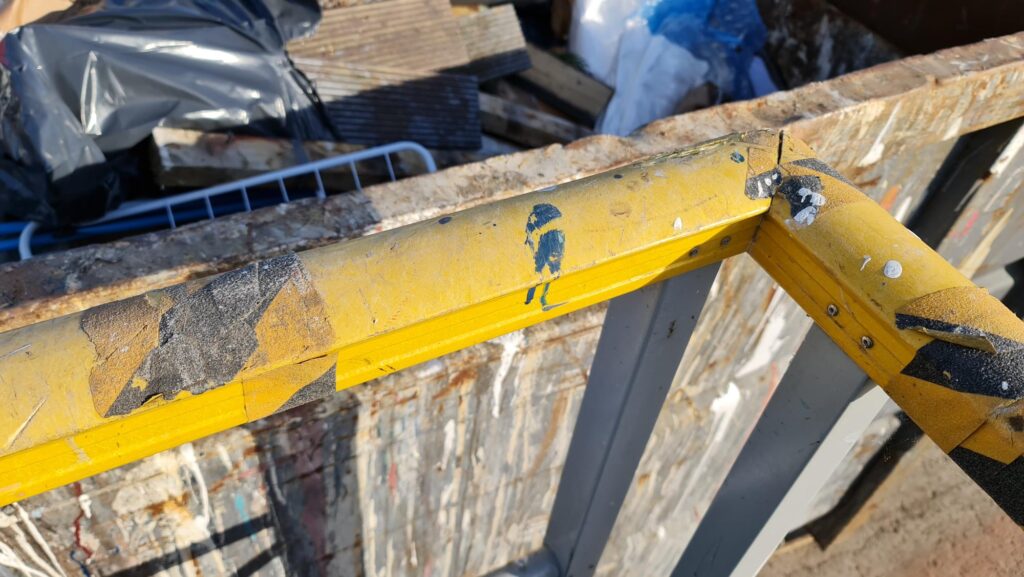
In an ideal world when the waste containers are being moved, the access steps are moved out of the way first. In an ideal world members of the public disposing of heavy items bring someone with them to help. Unfortunately we don’t live in an ideal world and the access stairs at recycling centres are subjected to a substantial amount of abuse every day by both operatives and visitors. Most of the damage has been to the handrails at the top of the steps.
One of the MAPs was actually hit by a vehicle, rendering it unsafe to use. But, by replacing some broken fixings and some damaged framework, it will be good to go in no time. GRP repairs don’t require welding equipment – just a few hand held power tools.
Continual Improvement
The London Energy steps are being repaired this week and some adjustments are being made to reduce the risk or further damage:
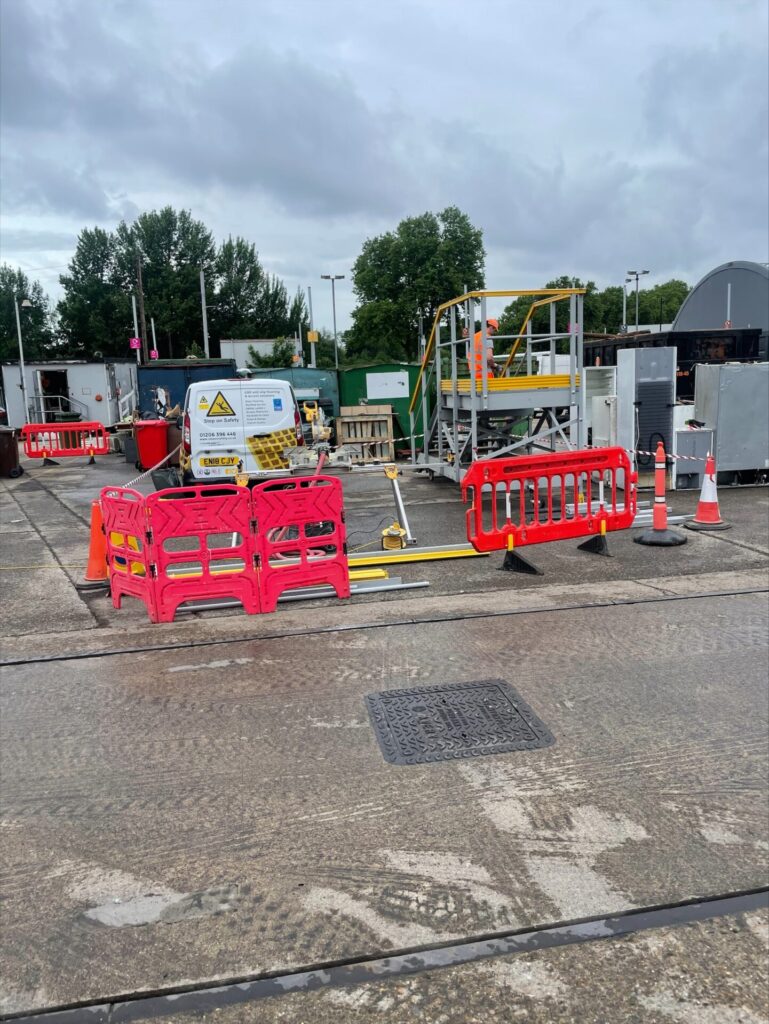
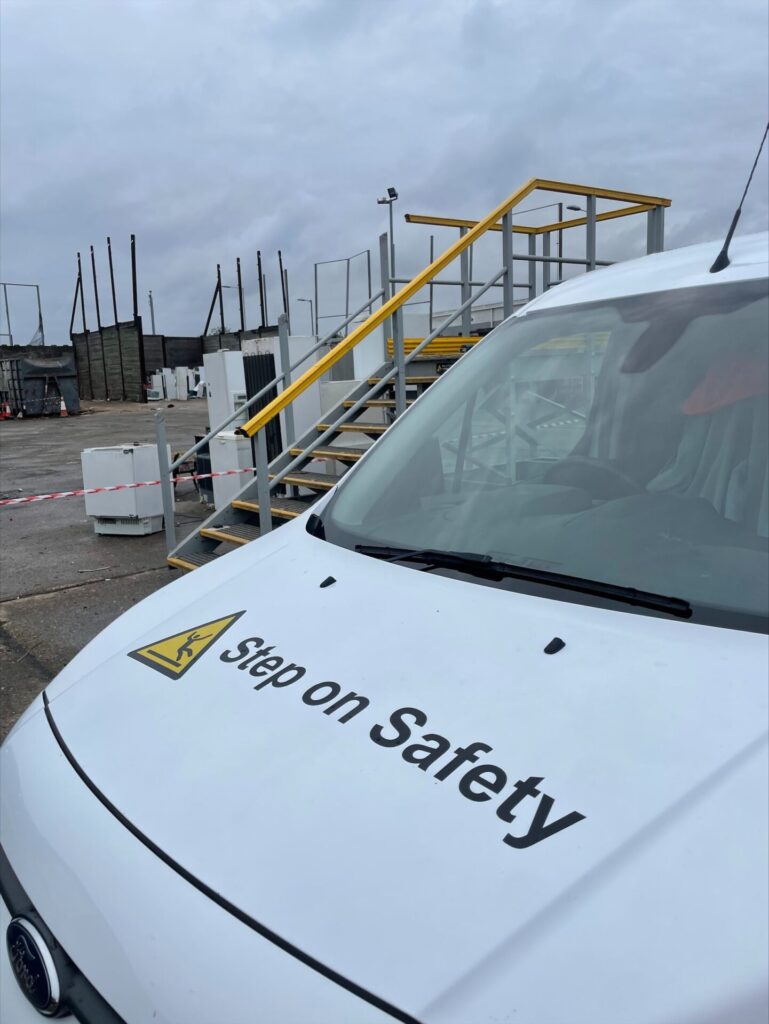
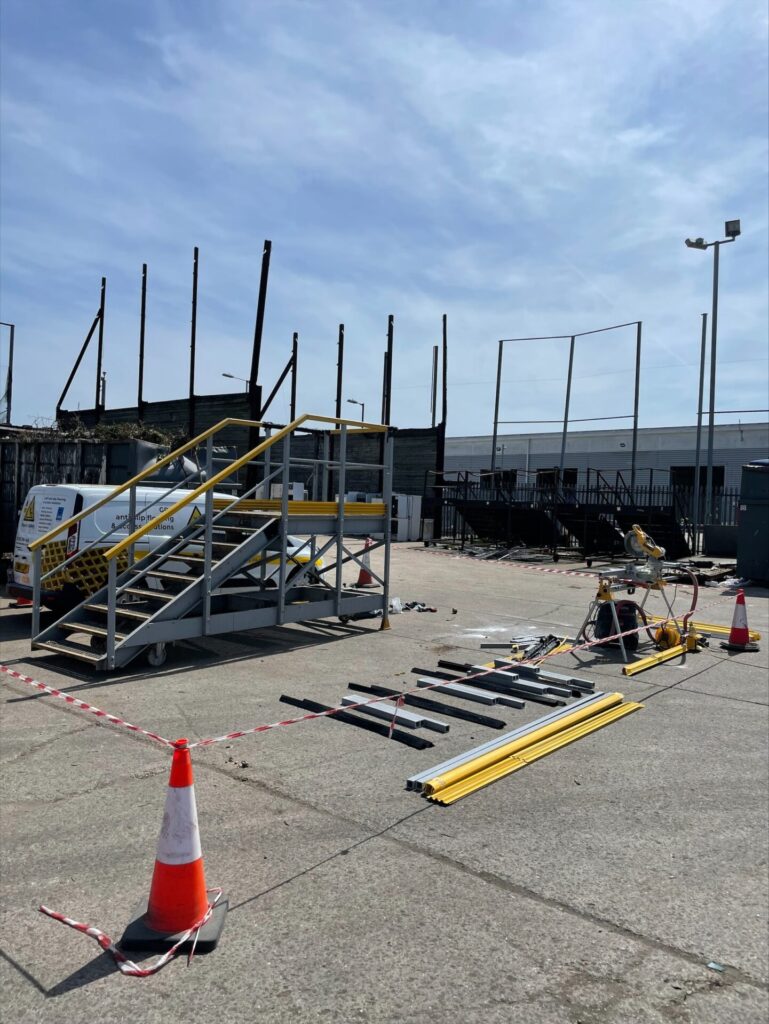
- We’re reducing the height of some of the handrail so that it sits below the edge of the skips – preventing people from balancing heavy objects on it as they lift them over the side.
- We’re reinforcing some of the handrail with GRP Box Profile inside the Ergonomic Top Rail. Handrail is normally designed in accordance with BS 7818 (1995) with a uniform horizontal load in mind – from people leaning or pushing against it. We’re strengthening it to withstand vertical point loads (fridges, hard core, etc) in case people still balance heavy items on it.
The changes we’re making are already standard on any stairs we now build for recycling centres. As an ISO 9001 certified business, we are constantly developing our products and specifications, learning how and where improvements can be made to ensure longevity. We work closely with our clients to understand exactly what they need and what challenges the future might present. And, whenever possible, we revisit old projects to see how our solutions are holding up and what – if any – improvements or changes we might make if we get a similar job in the future.
If you have an access requirement – whether it’s a typical one or a unique situation – you can be sure that we will do our utmost to come up with a solution that works. And that lasts.
Get in touch today to find out more.