What is Glass Reinforced Plastic?
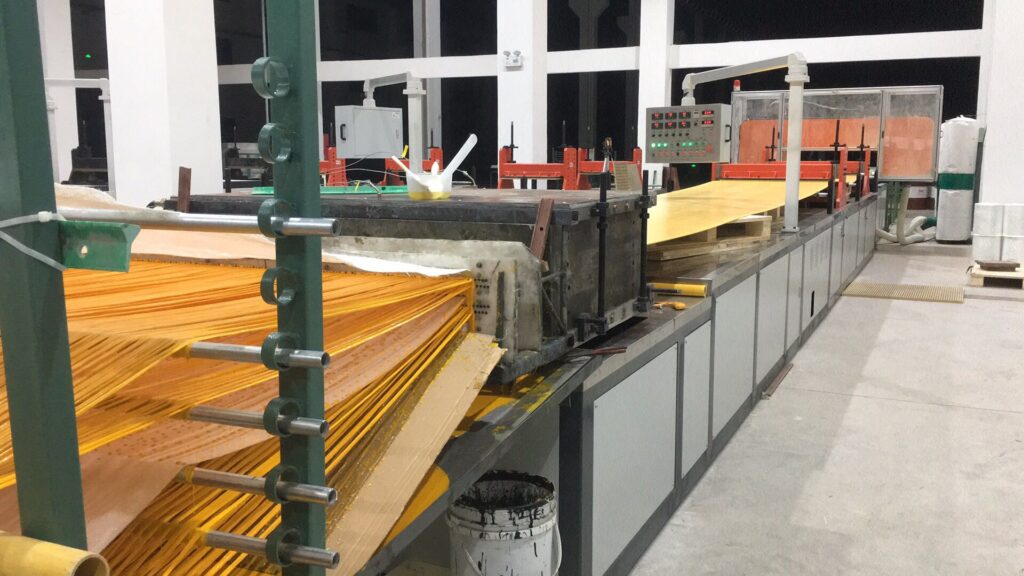
GRP stands for Glass Reinforced Plastic (or Polymer). You may also know it as FRP (Fibre Reinforced Plastic) or even as Fiberglass. It is a blend of recycled plastic and recycled glass with a tough waterproof resin to bond it all together. This mixture is then moulded into the required shape – whether that’s a panel of open mesh or grating (or waffle board) to use as flooring or fencing, or long, smooth profiles used to build the framework of a structure. An extra layer, embedded with sharp quartz grit, is often added to the top to create a slip-resistant surface that remains effective in wet, icy or even oily conditions.
The composite material was originally developed for the boating industry as a lightweight, tough, waterproof alternative to wooden hulls, it is now well-established within the construction industry and can be found in buildings, factories, utility plants, power stations, railway stations, marinas and docks across the globe. GRP manufacturing also takes place worldwide; China currently dominates the market in moulded GRP but India is catching up. The pultruded GRP Profiles we use are made in the UK.
As more and more industries explore the benefits of using GRP instead of steel, different types have been developed to cope with some of the world’s most inhospitable environments. They are made by using different qualities of resin to bond with the glass and plastic.
Qualities of Resin
Orthophthalic Resin (Ortho)
Ortho resins are based on orthophthalic acids and are a good, general purpose and inexpensive choice. They are most commonly used for applications that aren’t subject to high temperatures or highly corrosive environments
Isophthalic Resin (Iso)
GRP made with Iso resins are better suited to corrosive environments and can cope with higher temperatures. They have greater mechanical properties too which means they are the ones most commonly used when building structures. For this reason, they generally cost more to produce than the Ortho versions.
Vinyl Ester Resin
Much denser than Ortho or Iso resins, Vinyl Ester GRP products are more able to absorb impact without damage and are often used to reinforce structures made from Iso or Ortho resin.
Phenolic Resin
Grating made from Phenolic GRP is the latest and strongest version to date and can be found in the most hostile of environments including oil refineries, oil platforms, underground mining, railways and in shipping. It has the maximum fire resistance and emits little smoke or toxic fumes when burning – critical in enclosed spaces. Its reinforced structure can take exceptional loads – useful where large, uninterrupted spans need to be bridged.
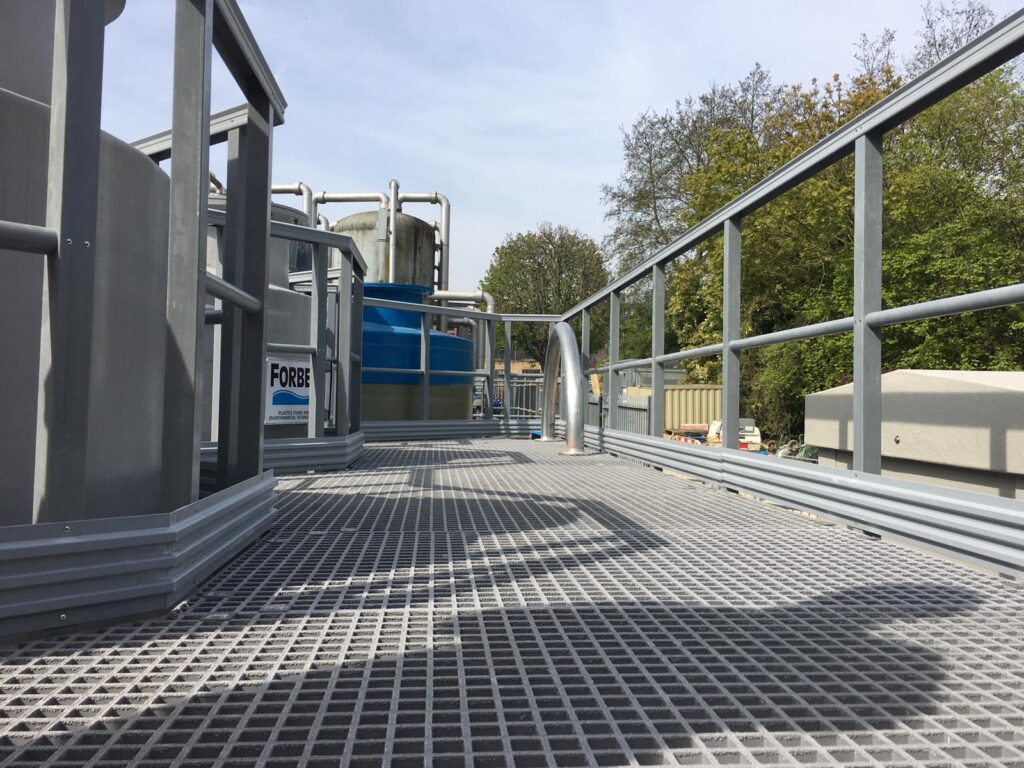
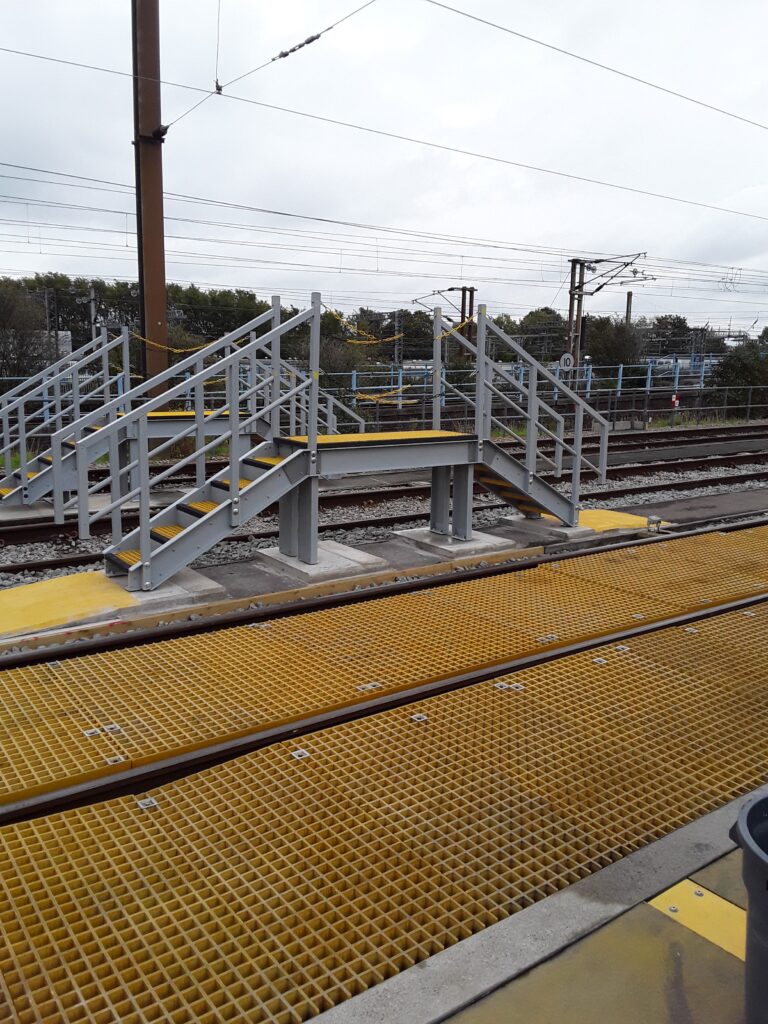
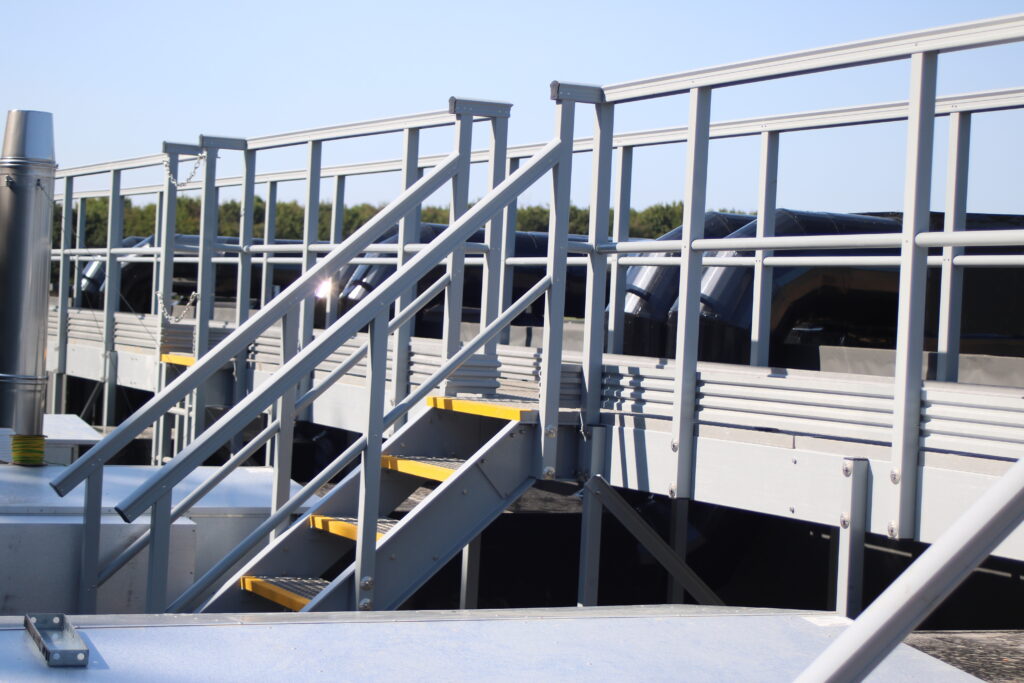
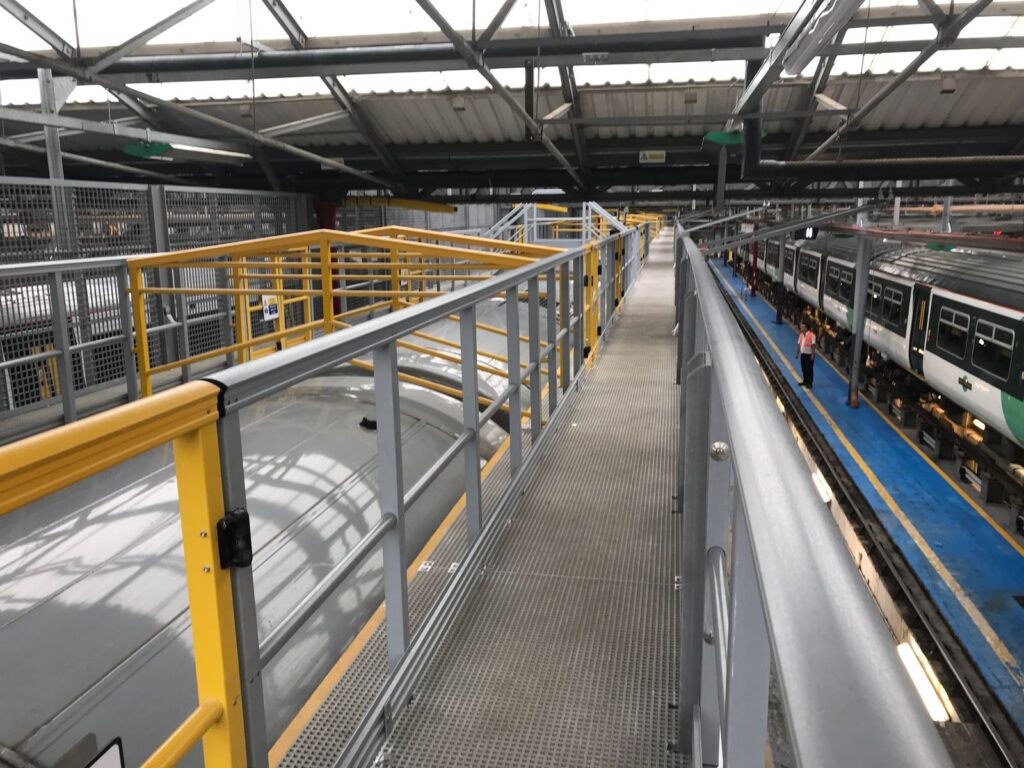
Characteristics of GRP?
More and more architects and developers are switching from steel to GRP alternatives; we took a look at the reasons why:
- Slip Resistant
QuartzGrip moulded fibreglass grating has an intergral, angular quarts gritted surface tested in accordance with BS7976-2. It provides an exceptional level of slip resistance in all direction. Lifespan depends on frequency of use.
- Chemical Resistant
GRP is resistant to a wide range of chemicals, across a wide temperature spectrum. It can also be made using different resin systems to achieve specific chemical resistance properties.
- Fire Resistant
All products contain a fire resistant additive and comply with Euro Class 1 and ISO 11925-2. Performance is equivalent to ASTM E84 Class A and BS EN 13501-1 Class Bfl-s1
- Quality Assured
Manufactured in accordance with our ISO 9001 accredited Quality Management System, the structural integrity of the material is high grade. A suggested lifespan of 25 years can be expected, based on a number of variables: environmental, installation process, maintenance, loading and traffic conditions.
- Lightweight & Durable
Weighing a fraction of the steel equivalents, GRP us lightweight in comparison and can be maneuvered into place without mechanical assistance. It’s exceptionally durable and has the ability to withstand impact, reducing the risk of permanent buckling or deformation.
- Self-Coloured
All QuartzGrip moulded fibreglass grating and GRP Profiles are pigmented throughout during manufacture and do not require any secondary treatment such as powder coating or paint spraying. There are a range of standard stock colours; bespoke colours are available upon request.
- UV Stable
All products are manufactured with a high quality UV inhibitor to prevent color degradation.
- Economical
In most cases, GRP equivalents to steel components are much cheaper to buy. Add to that, the reduction in handling and maintenance costs and GRP is the smart choice.
- It’s easy to cut
All that’s needed is a heavy duty saw. There are no sparks created when cutting GRP gratings, so there is no fire risk and no Hot Works permits are required
- It doesn’t conduct heat
GRP feels warmer than steel as it doesn’t absorb body heat, so it’s more comfortable to work around.
- It’s quieter
Running up or down a steel staircase is a noisy, clanging business; GRP Walkways and Staircases don’t resonate in the same way making for a less disruptive working environment. - 100% Recyclable
According to the European Composites Industry Association (EuCIA), GRP is 100% recyclable and can be reused in many different applications. GRP products can be professionally recycled to produce high-quality substitute fuels and reclaimed fibres. Furthermore, processed GRP waste is a high-grade alternative for the cement industry where it is used both as a fuel and as a mineral raw material (SiO2). Read more about GRP Sustainability here.